Materials Used in Wire Cloth and Mesh


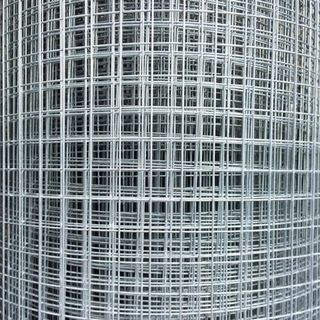
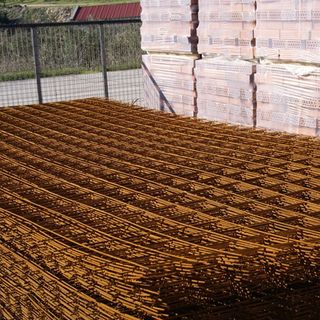
Wire cloth and wire mesh can be manufactured from any metal or alloy than can be drawn into wire that is suitable for weaving.
Industrial requirements to meet specific applications has resulted in the development of a broad spectrum of wire cloth materials. Each type of material has its own distinct properties that effect its performance in the particular application.
The selection of the material is dependent on the intended usage and consideration of various factors including:
The final application of the wire cloth pertaining to requirements of strength, abrasion resistance, chemical resistance, corrosion resistance, heat resistance or the suitability for use in food production etc.
Secondary processing such as suitability for forming, welding, heat treating, or the application of coatings.
The most commonly utilized materials in wire cloth weaving are listed here for reference purposes.
Industrial requirements to meet specific applications has resulted in the development of a broad spectrum of wire cloth materials. Each type of material has its own distinct properties that effect its performance in the particular application.
The selection of the material is dependent on the intended usage and consideration of various factors including:
The final application of the wire cloth pertaining to requirements of strength, abrasion resistance, chemical resistance, corrosion resistance, heat resistance or the suitability for use in food production etc.
Secondary processing such as suitability for forming, welding, heat treating, or the application of coatings.
The most commonly utilized materials in wire cloth weaving are listed here for reference purposes.
STEEL
High Carbon
High Carbon hard drawn steel is used when resistance to abrasion and impact is required. This material is commonly utilized in agriculture, coal, gravel, mining, sand and stone separating, sizing and sorting applications.Oil Tempered
Oil Tempered wire is specially tempered high carbon steel wire to provide greater strength and abrasion resistance, although its resistance to impact is somewhat lower than regular high carbon steel.Stainless Steel
With the addition of 11% or more chromium to steel, the alloy becomes non-staining under most conditions that corrode plain steel, thus the term stainless is applied.NON-MAGNETIC ALLOYS
Alloys containing chromium and nickel are not magnetic in the annealed condition although they become slightly magnetic when cold worked.
Type 304
Often referred to as "18-8" (18% chromium, 8% nickel) T-304 is the basic stainless alloy most commonly utilized for wire cloth weaving. It withstands outdoor exposure without rusting and resists oxidation at an elevated temperature up to 1400 Degrees Fahrenheit.Typical wire cloth applications include use with chemicals, food products, pharmaceuticals and exposure to moisture.
Type 304 L
Type 304 L is very similar to T-304, the difference being the reduced carbon content for better weaving and secondary welding characteristics.Type 309
A heat resistant alloy (23% chromium, 12% nickel) which is useful in temperatures up to 1700 Degrees Fahrenheit.Type 310
Retains good strength and toughness at high temperatures and may be used to advantage where a combination of strength, toughness and oxidation resistance is essential. Where reducing or carburizing conditions are encountered at high temperatures, T-310 is preferred.Type 310 has a coefficient of expansion slightly lower than most other chromium - nickel alloys.
Type 316
Stabilized by the addition of 2% molydbenum, T-316 is an "18-8" alloy.Type 316 has better resistance to pitting corrosion than the other chromium-nickel stainless steels where brines, sulphur-bearing water or halogen salts, such as chlorides are present. A valuable property of T-316 is high creep strength at elevated temperatures. Other mechanical properties and fabricating characteristics are similar to T-304.
Wire cloth woven of T-316 has extensive use in chemical processing when better corrosion resistance is required than the regular chromium-nickel types.
Type 316 L
Type 316 L is very similar to T-316, the difference being the reduced carbon content for better wire cloth weaving and secondary welding characteristics.Type 317
Similar to the basic alloy (18% chromium) but with a higher nickel (14%) and molybdenum (3%) content for increased corrosion resistance.Type 321
Has titanium added to reduce or eliminate chromium carbide precipitation resulting from welding or exposure to high temperatures. It is quite effective as a stabilizer although the over-all corrosion resistance is somewhat reduced.Type 321 wire mesh is normally used where secondary welding processes are not required.
Type 330
Similar to Incoloy, T-330 is a nickel-chromium alloy (35% nickel, 15% chromium) used for heat treating baskets suitable for temperatures up to 1650 ° Fahrenheit.Type 347
Similar on analysis to Type 321 except that columbium is used as an addition instead of titanium. Columbium is an effective stabilizer and does not appreciably reduce the over-all corrosion resistance as does titanium.Wire cloth woven of Type 347 is used when secondary welding procedures are required, in applications subject to corrosive environments.
MAGNETIC ALLOYS
Type 410
The general purpose alloy of the martensitic class containing 12.5% chromium. Heat treated T-410 has mechanical properties comparable to alloy steels such as SAE 4130.Type 410 possesses mild corrosion resistance as well as heat and oxidation resistance up to 1400º Fahrenheit.
Type 430
The general purpose alloy of the ferritic class and the most popular of straight chromium (17%) stainless steels. More commonly used for wire cloth production, T-430 is not heat treatable but is more resistant to chemical attack and high temperature than T-410.COPPER AND COPPER ALLOYS
Copper
Copper offers excellent electrical and thermal conductivity. It is non-magnetic, anti-sparking and is resistant to atmospheric corrosion, salt air and brine.Copper applications are limited due to its low tensile strength, poor resistance to abrasion and common acids.
Brass
High brass (70% copper, 30% zinc) and low brass (80% copper, 20% zinc) have much better abrasion resistance, better corrosion resistance and lower electrical conductivity when compared to copper.Bronze
Superior to low brass in resistance to corrosion, this alloy contains 90% copper and 10% zinc. The combination of lower tensile strength and better formability when compared to brass make bronze a popular alloy for window screening.Phosphor Bronze
This copper-tin (4% to 9% tin, approximately 0.25% phosphorous with the balance copper) alloy is corrosion, wear and tear resistant was frequently used in the past for fine mesh cloth.Phosphor Bronze is not suitable for exposure to hydrochloric acid or strong oxidizing agents.
ALUMINIUM AND ALUMINIUM ALLOYS
A unique combination of properties makes aluminum one of our most versatile wire cloth weaving materials. It is light in mass, yet some of its alloys have strengths greater than that of structural steel. It has high resistance to corrosion under the majority of service conditions and no colored salts are formed to stain adjacent surfaces or discolor products with which it comes into contact.
A word of caution should be mentioned in connection with the corrosion resistant characteristics of aluminum. Direct contacts should be avoided in the presence of an electrolyte; otherwise galvanic corrosion of the aluminum may take place in the vicinity of the contact area. Where other metals must be fastened to aluminum wire cloth the use of a bituminous paint coating or insulating tape is recommended.
A word of caution should be mentioned in connection with the corrosion resistant characteristics of aluminum. Direct contacts should be avoided in the presence of an electrolyte; otherwise galvanic corrosion of the aluminum may take place in the vicinity of the contact area. Where other metals must be fastened to aluminum wire cloth the use of a bituminous paint coating or insulating tape is recommended.
1100
Pure Aluminum in the woven form is typically used where its light weight and corrosion resistance is more important than strength.5056
Containing magnesium, manganese and chromium, this non-heat treatable alloy is used most often for weaving wire cloth. 5056 contains 5% magnesium providing good corrosion resistance (particularly in marine atmospheres) and greater strength.ALCLAD 5056
The wire has a core of 5056 Aluminum encased in pure Aluminum, a combination providing both strength and corrosion resistance.NICKEL AND NICKEL ALLOYS
Nickel
Nickel is noted for its corrosion resistance, good electrical conductivity and high heat-transfer properties. Wire mesh woven of nickel is used in pure food and drug processing among several other applications although nickel wire cloth is replaced frequently with stainless steel.Monel 400
This nickel-copper alloy contains approximately 67% nickel, 28% copper and 5% other elements. It is essentially non-corrodible. Monel is more resistant to oxidation than copper and more resistant to reducing conditions than nickel.Hastelloy B
This nickel based alloy is recommended for corrosion resistance to hydrochloric acid and hydrogen chloride gas, although it is usually not used for high temperature applications.Hastelloy C
Offering good corrosion resistance to strong oxidizing agents, this alloy performs well at elevated temperatures in the range of 1600º to 1800º Fahrenheit.Inconel 600
This alloy is high in nickel content (76% to 80%), combined with a chromium content of 14% to 16% is suitable high temperature applications where resistance to corrosion is required. Inconel is the preferred material for heat-treating baskets fabricated of woven wire cloth.Incoloy 800
Similar to T-330 stainless steel, Incoloy has superior corrosion resistance and strength.Nichrome I (60/16)
A high nickel (60%) alloy containing 16% chromium and 24% iron suitable for certain chemical conditions and for temperatures up to 1700º Fahrenheit.Nichrome V (80/20)
A higher nickel chromium alloy containing 80% nickel, 20% chromium, this material is suitable for severe chemical conditions and for elevated temperatures up to 2000º Fahrenheit.OTHER METALS
Rare metals such as columbium, gold, molydbenum, platinum, titanium and tungsten can be provided as specified.